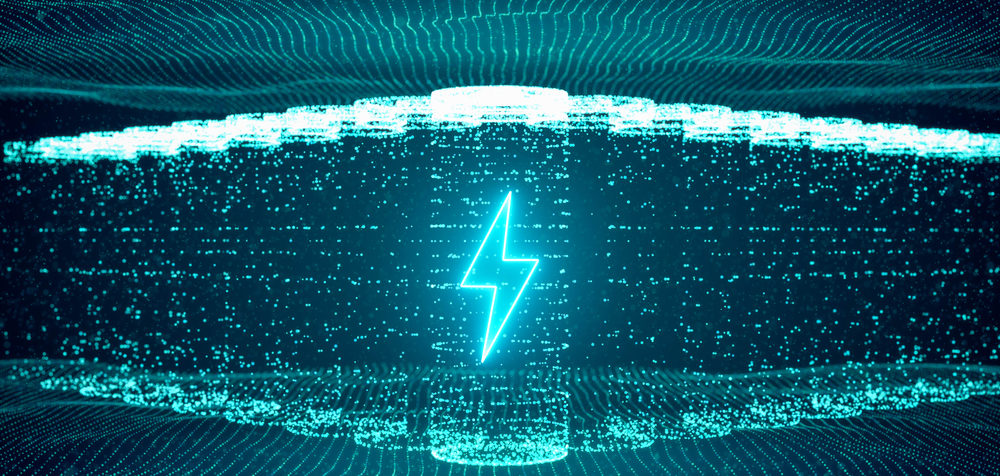
Rice University researchers have developed a technique that can quickly regenerate the graphite anode materials found in lithium-ion batteries so that they can be reused multiple times.
“The production of lithium-ion batteries in 2026 is expected to be five times what it was in 2017, and right now, less than 5% of them are recycled,” James Tour, professor at Rice University’s Department of Chemistry, Materials Science and NanoEngineering, said. “That puts a heavy load on the environment, as these spent batteries are processed, and the anodes are burned for energy or sent to landfills.”
The process uses a unique “flash” Joule heating process that can decompose inorganic salts – including lithium, cobalt, nickel, and manganese – from an anode. These can then be recovered by processing them with dilute hydrochloric acid. Flashing anodes degrades the solid-electrolyte interphase (SEI), which conducts lithium ions an also insulates the anode from detrimental reactions. The process then coats the remaining graphite particles with an ion-permeable carbon shell. This shell contributes to their future capacity, rate performance and cycling stability, making them more viable when compared to the expensive, high-temperature calcination technique currently in use.
When tested, the recycled, flashed anodes retained more than 77% of their capacity after 400 recharge cycles. The lab estimates that it would cost about US$118 to recycle one ton of untreated anode waste.
“We’re claiming our process can recover critical metals and recondition anodes in a far more environmentally and economically friendly manner,” stated Tour. “Beyond the spent graphite anodes, we are confident that the cathodes, the electrolytes, and their mixtures can be effectively recycled or reconditioned by our method,” added Weiyin Chen, lead author of the study.