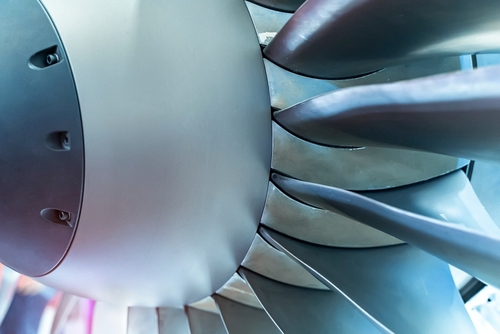
Engineers at MIT’s necstlab have developed a new technique called nano stitching that promises to radically change how composite materials are constructed. The research group at necstlab – pronounced next lab – explores new concepts in engineered materials and structures.
Advanced composites – also called thin-ply carbon fiber laminates – are used to construct lighter and stronger aircraft in order to save on fuel, reduce aircraft emissions, require less repairs, and increase their longevity. Advanced composites are engineered materials made from high-performance fibers that are embedded in polymer sheets, which are stacked and pressed into one multilayered, lightweight, and durable material. But, like any material formed of disparate materials, the space between layers can crack and spread, eventually leading to a breakdown of the structure.
In the process of nano stitching, the team used chemical vapor deposition to create nanotubes that were deposited between composite layers. These densely packed nanofibers are able to grip and hold the layers together, preventing the layers from peeling or shearing apart. When this reinforcement method was tested, the researchers found promising results.
The team evaluated how crack-resistant nano stitching makes an advanced composite material – such as would be used in aircraft, automotive manufacturing, and shipbuilding. Under testing, they cracked the composite’s edge at the outset to determine if that crack would spread.
“We wanted to see whether there might be synergy between our nano stitching and this thin-ply technology, since it could lead to more resilient aircraft, high-value aerospace structures, and space and military vehicles,” said Brian Wardle, professor of aeronautics and astronautics at MIT. “The nanostitched samples were up to 62 percent tougher and more resistant to cracks compared with the same advanced composite material that was held together with conventional polymers.”
“You could have selective reinforcement of problematic areas, to reinforce holes or bolted joints, or places where delamination [separation or cracks] might happen,” said Carolina Furtado, the study’s first author. “This opens a big window of opportunity.”