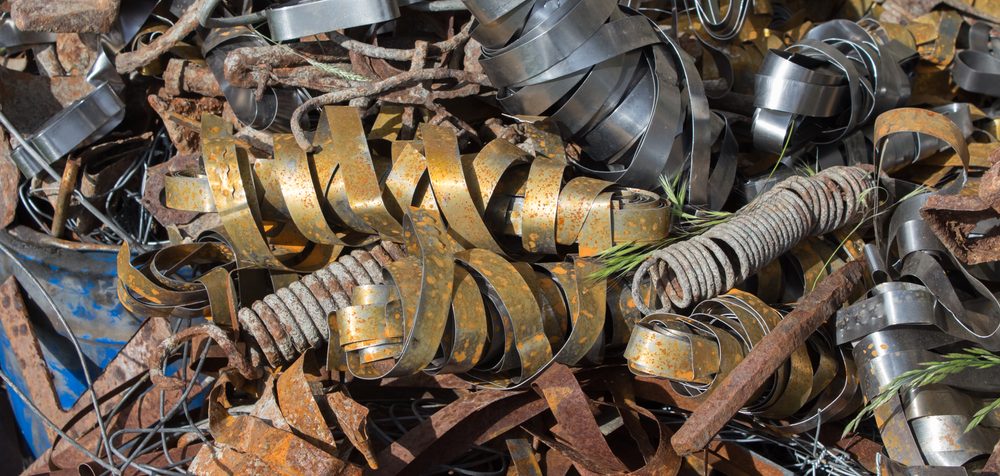
A team of researchers from the University of Nottingham has developed a method to convert metal waste into a catalyst for producing hydrogen from water. In the future, this new technique could enhance the sustainability of hydrogen production.
Though hydrogen is highly desirable as it is a clean fuel that only produces water vapor as a byproduct of its combustion, most hydrogen production methods rely on fossil fuel feedstock. The electrolysis of water, which only requires water and electricity, is a promising method for the efficient and clean production of hydrogen. But, the process of water electrolysis requires rare and expensive elements – such as platinum – as a catalyst for splitting the water.
The team discovered that the surface of swarf – a byproduct of the metal machining industry – is textured with tiny grooves on a nanoscale level. This textured surface can anchor atoms of platinum or cobalt, leading to an efficient electrocatalyst that can split water into hydrogen and oxygen.
“Industries in the UK alone generate millions of tons of metal waste annually. By using a scanning electron microscope, we were able to inspect the seemingly smooth surfaces of the stainless steel, titanium, or nickel alloy swarf, “ said Jesum Alves Fernandes, team lead . “To our astonishment, we discovered that the surfaces had grooves and ridges that were only tens of nanometres wide. We realized that this nanotextured surface could present a unique opportunity for the fabrication of electrocatalysts.”
The team used magnetron sputtering to create a platinum atom “rain” on the surface of the swarf. The platinum atoms then came together into nanoparticles that fit tightly into the nanoscale grooves.
“It is remarkable that we are able to produce hydrogen from water using only a tenth of the amount of platinum loading compared to state-of-the-art commercial catalysts. By spreading just 28 micrograms of the precious metal over 1 cm² of the swarf, we were able to create a laboratory-scale electrolyzer that operates with 100% efficiency and produces 0.5 liters of hydrogen gas per minute just from a single piece of swarf,” said Dr. Madasamy Thangamuthu, a Postdoctoral Researcher at the University of Nottingham.
The group is partnering with AqSorption Ltd – a Nottingham-based company specializing in electrolyzer design and fabrication -to scale up their technology.