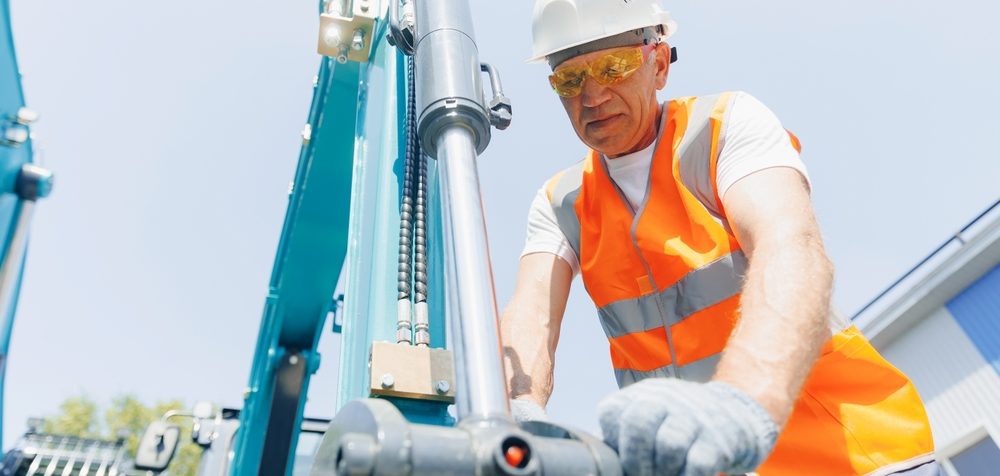
Researchers at Stanford University have developed a spring-assisted actuator that can augment electric motors to make them much more efficient at performing dynamic movements.
The standard electric motor was designed for steady, ongoing activities, not for energy efficiency when performing dynamic tasks. Stanford’s new actuator uses springs and clutches to accomplish a variety of these tasks with a fraction of the energy usage.
“Rather than wasting lots of electricity to just sit there humming away and generating heat, our actuator uses these clutches to achieve the very high levels of efficiency that we see from electric motors in continuous processes, without giving up on controllability and other features that make electric motors attractive,” said Steve Collins, associate professor of mechanical engineering and senior author of the paper.
Along with harnessing the ability of springs to produce force without using energy, the springs can engage and disengage quickly and efficiently by using a series of electroadhesive clutches. Each rubber spring is sandwiched between two clutches: one that connects the spring to the joint to assist the motor and one that locks the spring in a stretched position when it’s not being used. The clutches contain two electrodes – one attached to the spring and one attached to the frame or motor – that slide smoothly past each other when they aren’t active. To engage a clutch, the researchers apply a large voltage to one of its electrodes, drawing them together. To release the spring, the electrode merely needs to be grounded, dropping its voltage back to zero.
“They’re lightweight, they’re small, they’re really energy efficient, and they can be turned on and off rapidly,” said Erez Krimsky, lead author of the paper. “And if you have lots of clutched springs, it opens up all these exciting possibilities for how you can configure and control them to achieve interesting outcomes.”
Motion tests – including rapid acceleration, changing loads, and smooth, steady movement – were conducted with the actuator. During every task, the new actuator used at least 50% less power than a standard electric motor and, in the best case, reduced power consumption by 97%.
The team is now working on shortening the timeframe required for the actuator’s controller to calculate the most efficient way to use the combination of springs to accomplish a new task. In the future, they envision a system capable of learning from previous tasks, creating a growing database of increasingly efficient movements and using artificial intelligence to intuit how to effectively accomplish something new.
“There are a bunch of little control and design tweaks we’d like to make, but we think that the technology is really at a place where it’s ready for commercial translation,” Collins said. “We’d be excited to try to spin this out from the lab and start a company to begin making these actuators for the robots of the future.”