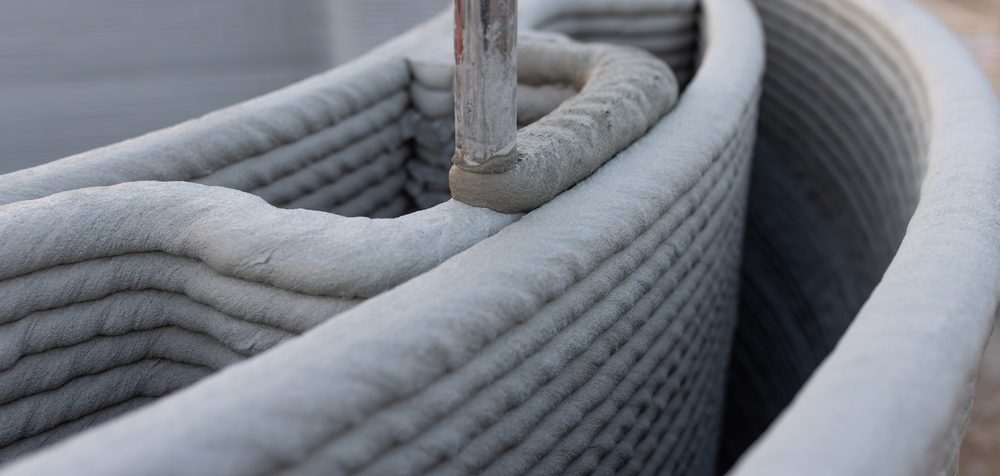
The first fire-resistant, onsite-built, concrete accessory dwelling unit (ADU) will soon be constructed in Northern California using a robotic 3D printer.
ADUs can be a cost-effective way to address the current housing shortage issue in the US, but traditional 3D printing methods have not been suitable for their construction as they require large machines that cannot fit in small lots.
“Our compact modular robotic 3D printer overcomes these limitations, enabling 3D construction in people’s backyards,” stated Ziyou Xu, founder and CEO of RIC Technology. “This marks a milestone in the housing industry, expanding the scope of concrete 3D printing’s application in constructing affordable housing.”
The new ADU will be built in Walnut Creek, CA and will be non-combustible and fire-resistant in response to the wildfire crisis in the state.
“3D printing is well-suited for constructing fire-resistant homes due to the non-combustible nature of the concrete we use to print,” said Xu.
The exterior walls of the ADU will be 3D printed using concrete, which is non-combustible. The roof will be made from steel and sure-boards, rather than the typical wooden structural roofs found in most 3D printed buildings.
“The ADU will be built without a single piece of wood or nail – no ‘fuel’ on the main structure,” said Aaron Liu, CEO of Builtech Construction Group, the project leader. “So we significantly minimize the likelihood of fire entering the home, enhancing the safety of the structure.”
It’s hoped that the successful execution of the Walnut Creek project could pave the way for further collaborations with local governments and fire departments – potentially extending fire-resistant construction to more communities vulnerable to wildfires.