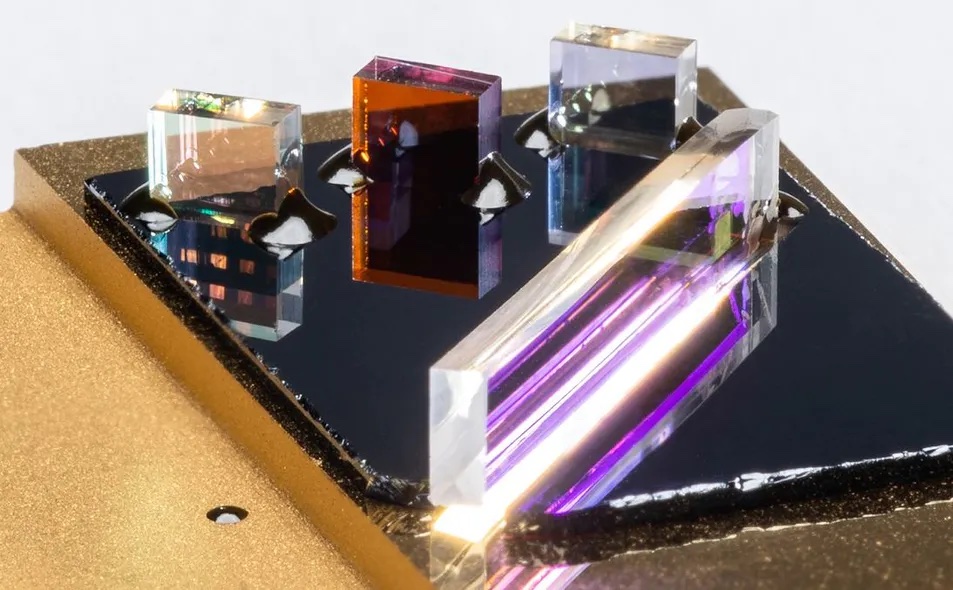
Researchers at the Charles Stark Draper Laboratory have developed new techniques to ruggedize electro-optical components for assured positioning, navigation, and timing (PNT) systems that are required to operate in environments with challenges such as extreme temperature, shock, and vibration. PNT data is used by the military for many kinds of missions, systems, and weapons – especially in aerospace and defense applications where Global Positioning System (GPS) satellite signals are unavailable.
Draper approached the challenge by designing new manufacturing methods for the electro-optical devices embedded within PNT devices. They reduced the complexity, labor requirements, and manufacturing costs of assembling and packaging electro-optics to make them better suited for systems intended for operation in harsh environments.
Current assembly methods rely on robotic alignment and bonding of several optical components and individual miniature mounts to a ceramic substrate. The reliance of adhesives to bond components to a substrate can make components vulnerable to environmental extremes, as many adhesives are sensitive to temperature and humidity, and difficult to dispense and manipulate at the microscale.
Draper researchers opted to fabricate silicon optical benches – wafer-level platforms composed of precision-etched surface features – which use a passive alignment method that requires fewer steps. Lenses and beam splitters can be placed onto the etched silicon surface where they are fabricated into 3D shapes. These 3D shapes register and anchor the optical components, and then simultaneously fuse them in a one melt-and-cool step.
This new manufacturing method appears to be a highly accurate way to assemble multiple microscale optical components extremely close together within a single device.