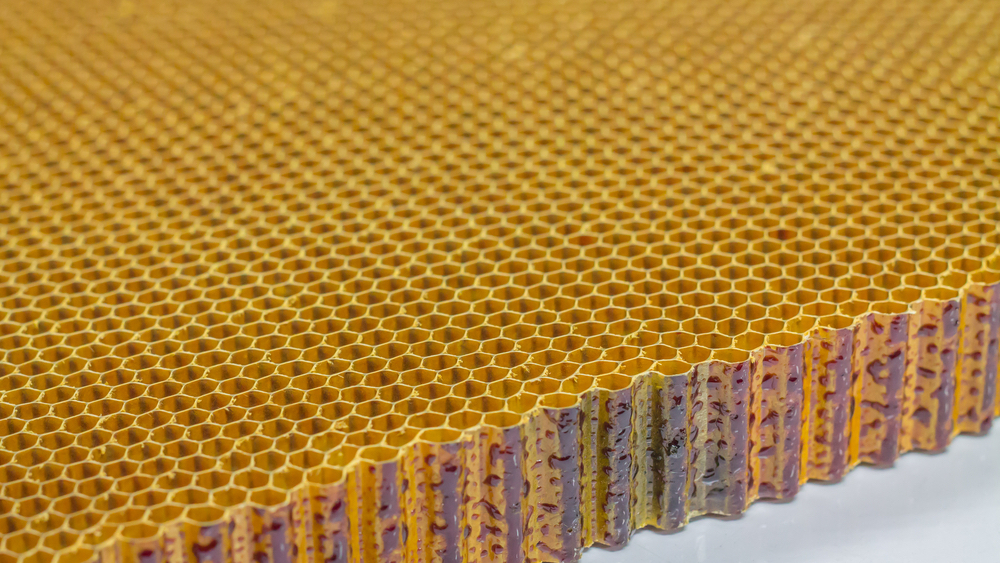
Researchers at the Australian Defense Science and Technology Group are investigating the potential of using drones to inspect subsurface damage in composite aircraft materials.
Composites materials are increasingly used in aircraft construction as they possess a high stiffness and strength-to-weight ratio, which affords reductions in aircraft weight, fuel consumption, and construction costs. They are more resistant to fatigue, but more vulnerable to impacts from such sources as hailstones, bird strikes, and runway debris. Low energy impacts are of particular interest as they can leave a surface unmarked yet cause significant damage inside – this type of damage is referred to as “barely visible impact damage” (BVID). As BVID’s are unpredictable and difficult to detect visually, they pose a challenge for current inspection practices such as manual ultrasonic testing (UT). As this method is time-consuming if the location of impact is not known routine screening for damage using UT is not undertaken by the industry, which means that subsurface damage can go unnoticed.
The team examined the feasibility of a drone-based inspection system that uses thermal techniques to detect defects over wide areas. Active thermography is a technique that employs a thermal imager to capture the heat signatures of a structure, which is then analyzed to identify potential subsurface defects. Sections that exhibit a temperature evolution different from that of surrounding structure can suggest the presence of a subsurface defect. A drone was equipped with line scan thermography (LST) – where a focused line of light is scanned across the structure while a thermal imager records the cooling profile. To avoid potential hazards due to proximity of the drone to the aircraft, while still collecting valid data, a reflector was installed that could maintain a highly concentrated beam of light at a distance of 500 mm.
Tests were conducted to inspect composite materials with both simulated and real impact damage and the researchers were able to inspect a full aircraft wing within a relatively short time. The results were published here: Remote Line Scan Thermography for the Rapid Inspection of Composite Impact Damage, in the journal Composite Structures.