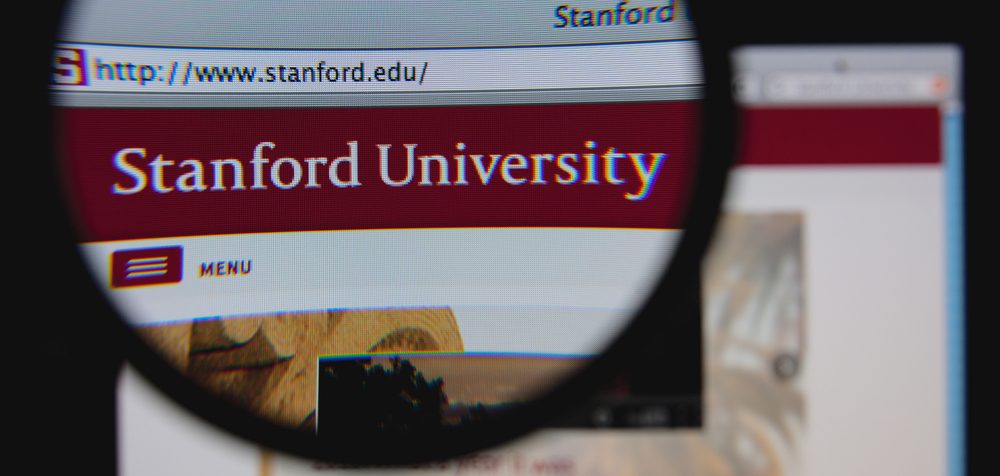
Researchers at Stanford University have developed an efficient processing technique that can 3D print up to 1 million highly detailed and customizable microscale particles per day. These particles have a wide range of uses in many fields, including drug and vaccine delivery, microelectronics, microfluidics, and abrasives for intricate manufacturing.
“We can now create much more complex shapes down to the microscopic scale, at speeds that have not been shown for particle fabrication previously, and out of a wide range of materials,” said Jason Kronenfeld, lead author of the paper.
The new printing process is an improvement on the technique – called continuous liquid interface production (CLIP) – that was developed by Joseph DeSimone, the Sanjiv Sam Gambhir Professor in Translational Medicine at Stanford Medicine and corresponding author of the paper, and his team. CLIP uses UV light, projected in slices, to cure resin rapidly into the desired shape. The technique uses an oxygen-permeable window above the UV light projector. This creates a “dead zone” that prevents liquid resin from curing and sticking to the window. As a result, delicate features can be cured without ripping each layer from a window, leading to faster particle printing.
“Using light to fabricate objects without molds opens up a whole new horizon in the particle world,” said DeSimone. “And we think doing it in a scalable manner leads to opportunities for using these particles to drive the industries of the future. We’re excited about where this can lead and where others can use these ideas to advance their own aspirations.”
To mass produce these uniquely shaped particles, they created an “assembly line”that begins with a film that is carefully tensioned and then sent to the CLIP printer. At the printer, hundreds of shapes are printed at once onto the film and then the assembly line moves along to wash, cure, and remove the shapes. Finally, the empty film is rolled back up, hence the name roll-to-roll CLIP, or r2rCLIP. Prior to r2rCLIP, a batch of printed particles would need to be manually processed, which was a slow and labor-intensive process. The automation of r2rCLIP now enables unprecedented fabrication rates of up to 1 million particles per day.
The researchers expect that the r2rCLIP process will see wide adoption by other researchers and industry partners.
“There’s a wide array of applications, and we’re just beginning to explore them,” said Maria Dulay, senior research scientist in the DeSimone lab and co-author of the paper. “It’s quite extraordinary, where we’re at with this technique.”