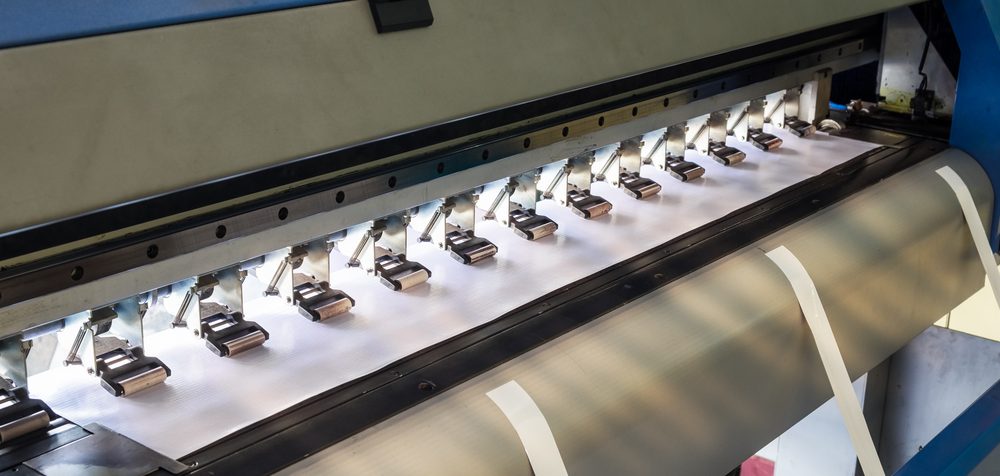
Researchers from MIT, Inkbit – an the MIT spinout, and ETH Zurich have designed a 3D inkjet printing system that not only expands the range of materials available, but also demonstrates a much higher speed than traditional systems.
Traditional 3D inkjet printing systems use nozzles to deposit drops of resin, smoothed over with a scraper or roller and then curved with UV light. The smoothing process, however, limits the materials that can be used.
This new printing process – called vision-controlled jetting – uses computer vision, making it a contactless system. It utilizes four high-frame-rate cameras and two lasers to scan the print surface continuously. The computer vision system converts the image into a high-resolution depth map, then compares the depth map to the CAD (computer-aided design) model of the part being fabricated, to guide the 16,000 nozzles in real-time.
“Our key insight here was to develop a machine vision system and completely active feedback loop,” said Wojciech Matusik, co-author of the study. “This is almost like endowing a printer with a set of eyes and a brain, where the eyes observe what is being printed, and then the brain of the machine directs it as to what should be printed next.”
As mechanical smoothing is no longer required, slow-curing materials such as thiol-based materials may be used. These are useful where greater elasticity, durability, or longevity are needed than the acrylates typically used in 3D printing can provide.
“There is an amazing number of new types of materials you can add to this technology. This allows us to bring in whole new material families that couldn’t be used in 3D printing before,” stated Matusik.
Additionally, the automatic system makes adjustments without stopping or slowing the printing process, making this printer about 660 times faster than a comparable 3D inkjet printing system.