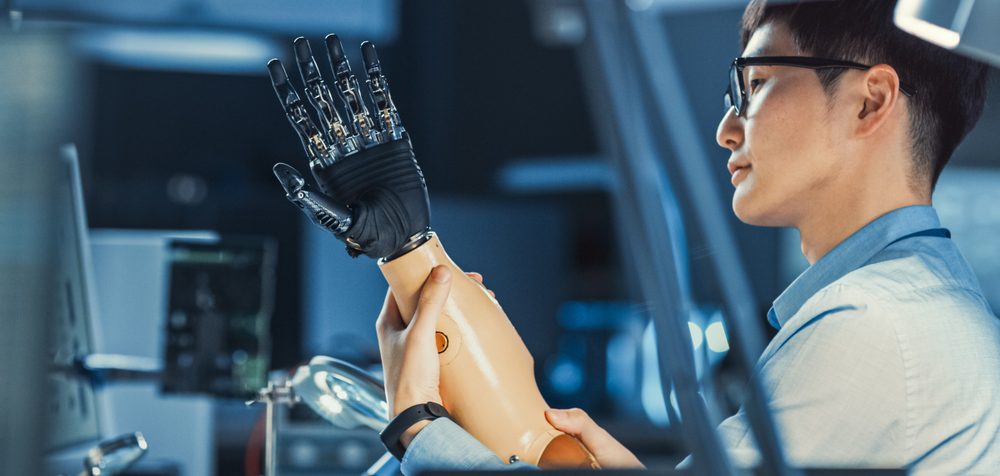
An international team of researchers, led by Pennsylvania State University, has taken a large step towards the creation of artificial muscles by developing a new ferroelectric polymer that efficiently converts electrical energy into mechanical strain. The material has a potential for use in medical devices, advanced robotics, and precision positioning systems.
Mechanical strain – how a material changes shape when force is applied – is vital to an actuator’s performance. Actuator materials, which change or deform when an external force such as electrical energy is applied, are typically rigid, but soft actuators – such as ferroelectric polymers – display higher flexibility, strength, and environmental adaptability.
“Potentially we can now have a type of soft robotics that we refer to as artificial muscle,” said Qing Wang at Penn State professor and co-corresponding author of the study. “This would enable us to have soft matter that can carry a high load in addition to a large strain. So that material would then be more of a mimic of human muscle, one that is close to human muscle.”
Ferroelectric polymers exhibit a tremendous amount of the electric-field-induced strain needed for actuation. This property, along with a high level of flexibility, reduced cost compared to other ferroelectric materials, and low weight, shows great promise for use in the field of soft robotics.
“In this study, we proposed solutions to two major challenges in the soft material actuation field,” said Wang. “One is how to improve the force of soft materials. We know soft actuation materials that are polymers have the largest strain, but they generate much less force compared to piezoelectric ceramics.”
The second challenge arises from the ferroelectric polymer’s need for a very high driving field, which is necessary to generate the shape change in the polymer required for the ferroelectric reaction to become an actuator. To address this challenge, the team developed a percolative ferroelectric polymer nanocomposite. By incorporating nanoparticles into a type of polymer – polyvinylidene fluoride – an interconnected network of poles within the polymer was created. This network enabled a ferroelectric phase transition to be induced at much lower electric fields than would normally be required.
“Typically, this strain and force in ferroelectric materials are correlated with each other, in an inverse relationship,” Wang said. “Now we can integrate them together into one material, and we developed a new approach to drive it using the Joule heating. Since the driving field is going to be much lower, less than 10%, this is why this new material can be used for many applications that require a low driving field to be effective, such as medical devices, optical devices, and soft robotics.”