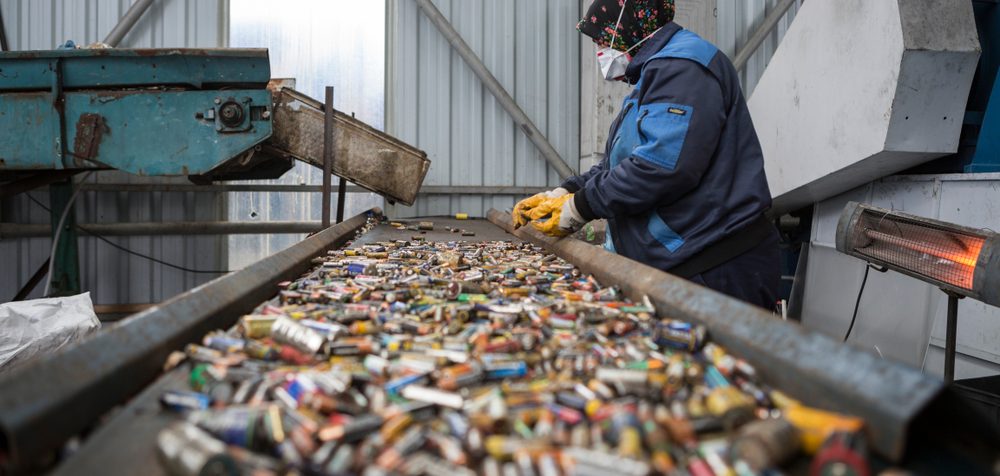
Scientists at Karlsruhe Institute of Technology (KIT) in Germany have developed a novel recycling method that can recover up to 70% of lithium from battery waste. Their technique does not use corrosive chemicals, high temperatures, or require prior sorting of materials. The method combines mechanical processes with chemical reactions and enables inexpensive, energy-efficient, and environmentally compatible recycling of any type of lithium-ion battery.
“The method can be applied for recovering lithium from cathode materials of various chemical compositions and, hence, for a large range of commercially available lithium-ion batteries,” said Dr. Oleksandr Dolotko of IAM-ESS and HIU, the first author of the publication. “It enables inexpensive, energy-efficient, and environmentally compatible recycling.”
Currently, recycling the lithium in rechargeable batteries involves either heating them to high temperatures or treating them with concentrated acids and organic solvents. Estimates for how much lithium is recycled vary, but some calculations suggest that perhaps only 15% of the metal in batteries is recovered.
KIT’s novel technique uses aluminum, which is already found in the cathode, as a reducing agent in the mechanochemical reaction. The researchers first ground the battery waste, then had it react with aluminum to create metallic composites with water-soluble lithium compounds. The lithium was then recovered by dissolving the water-soluble compounds in water and then heating to remove the water through evaporation.
This recovery method is highly energy efficient, as the mechanochemical reaction takes place at ambient temperature and pressure. It is also simple, which is expected to facilitate its use on an industrial scale.
The team is composed of researchers from the Energy Storage Systems Department of KIT’s Institute for Applied Materials (IAM-ESS), the Helmholtz Institute Ulm for Electrochemical Energy Storage (HIU) established by KIT in cooperation with Ulm University, and EnBW Energie Baden-Württemberg AG.