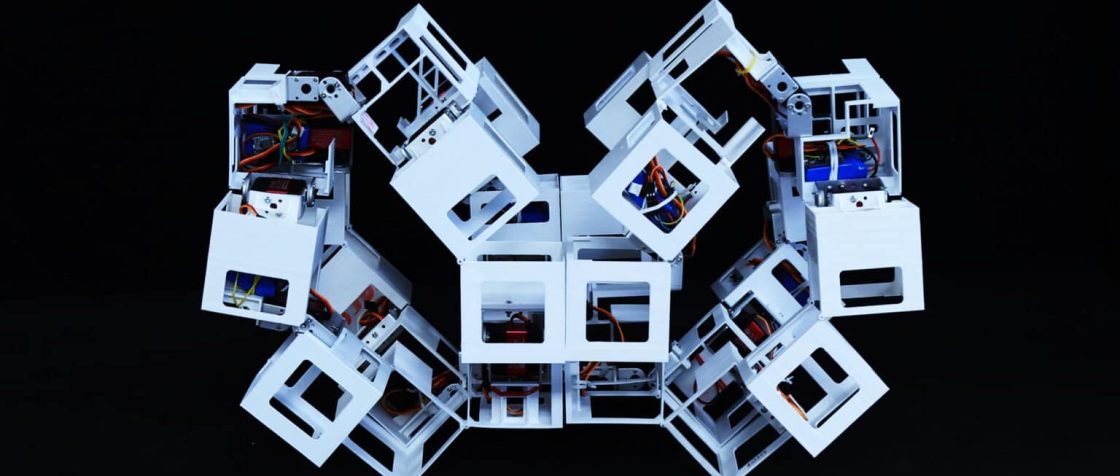
A research team at North Carolina State (NC State) University has created shape-shifting ‘Transformer’ robots that use just three active motors to change a single plastic cubed structure into over 1,000 different shapes. They expect that the technology could lead to the creation of artificial systems that can change shape and bear loads, such as adaptable robotic structures for use in space.
“The question we’re asking is how to achieve a number of versatile shapes with the fewest number of actuators powering the shapeshifting. Here we use a hierarchical concept observed in nature – like layered muscle fibers – but with plastic cubes to create a transforming robot,” said Jie Yin, associate professor of mechanical and aerospace engineering at NC State and co-corresponding author of the study.
Using a 3D printer, the researchers assembled 36 hollow plastic cubes with spinning hinges, with some hinges secured with metal pins, while others were turned on wirelessly by a motor. With just three active motors, the researchers were able to reposition the cubes into over 1,000 different configurations. These shapes included multistory buildings, bridge-like structures, and tunnel-like structures. Manipulating how the structure’s shape changes allows them to move forward, backward, and sideways. The bots may also change shape relatively quickly, going from being flat or totally open to being a larger cube that resembles a box or is fully closed. The bots are capable of lifting three times their own weight.
In future, the researchers aim to further enhance the transformer bots and they are currently working to create a more robust structure capable of bearing larger loads.
“We think these can be used as deployable, configurable space robots and habitats. It’s modular, so you can send it to space flat and assemble it as a shelter or as a habitat, and then disassemble it,” said Antonio Di Lallo, an NC State postdoctoral researcher and co-first author of the paper.