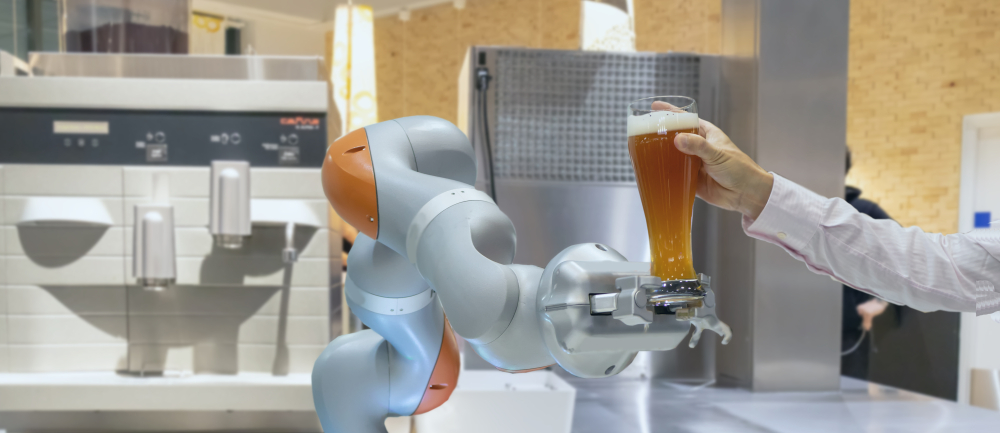
The University of Bristol’s Department of Engineering Mathematics is working with simple sponges to enhance the way robots grasp objects. The use of an easy-to-make sponge-jamming device can assist stiff robots handle delicate items carefully by mimicking the nuanced touch – or variable stiffness – of a human. The device could be used in industrial robots in scenarios requiring the handling of fragile substances, and possibly for use in service robots to make human-robot interaction safer.
Variable-stiffness devices are known to be potential solutions for contact compliance on hard robots to reduce damage, or for improving the load capacity of soft robots. When squeezed, silicone sponge – which is a cheap and easy-to-fabricate material – stiffens, turning it into a variable-stiffness device.
“Stiffness, also known as softness, is important in contact scenarios. Robotic arms are too rigid so they cannot make such a soft human-like grasp on delicate objects, for example, an egg.” explained lead author Tianqi Yue. “What makes humans different from robotic arms is that we have soft tissues enclosing rigid bones, which act as a natural mitigating mechanism. In this paper, we managed to develop a soft device with variable stiffness, to be mounted on the end robotic arm for making the robot-object contact safe.”
The team has future projects planned to make the device achieve variable stiffness in multiple directions, including rotation.
“We managed to use a sponge to make a cheap and nimble but effective device that can help robots achieve soft contact with objects. The great potential comes from its low cost and lightweight. We believe this silicone-sponge-based variable-stiffness device will provide a novel solution in industry and healthcare, for example, tunable-stiffness requirements on robotic polishing and ultrasound imaging,” said Yue.