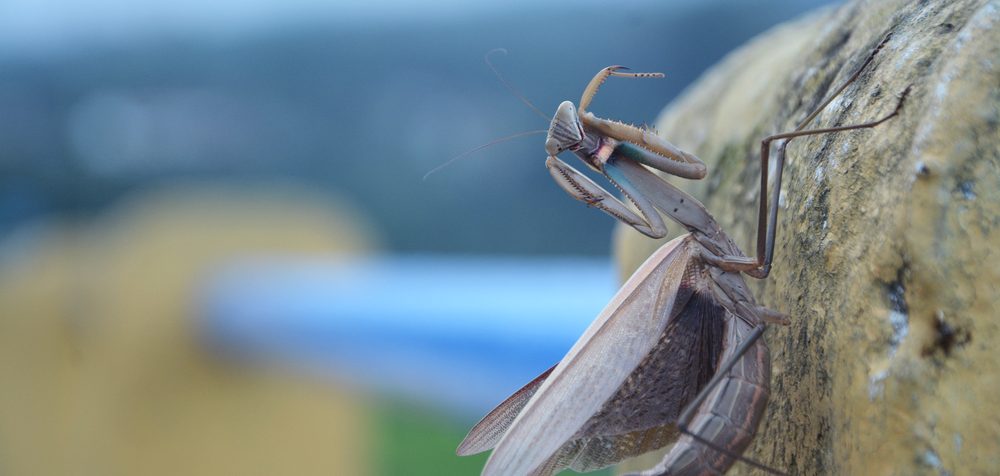
A research team led by Andrew Reid from the University of Strathclyde in Glasgow, Scotland is experimenting with 3D printing to create microphones inspired by insect ears. Such microphones could better pinpoint a sound’s direction than the equipment currently in use, and could be useful where a sound sensor is needed to quickly detect specific signals without consuming a lot of energy, or requiring much data or hardware.
Current technology is based on how we, as humans, detect sound directionality. Large animals have ears far enough apart to let them distinguish the differences in timing when a sound reaches one ear relative to the time it takes to reach the other. Their brains are then able to use this information to estimate the direction from which the sound came. However, insects’ ears are very close together, so they must rely on other ways of processing the sound.
Previous attempts at mimicking insect ears’ functionality used silicon microelectromechanical systems (MEMS) to try to copy insect structures. However, the resulting devices lacked the necessary flexibility and the microscopic 3D structural variations seen in real insect ears. Reid’s team is using 3D printing to more faithfully copy insect ears. They have 3D printed a variety of membranes to copy a range of insect tympana – thin sheets of tissue similar to the human eardrum. The base material for these membranes is a flexible hydroge, such as polyethylene glycol diacrylate. The membranes also include a piezoelectric material such as the perovskite oxide crystal known as PMN-PT, which can convert acoustic energy to electric signals, and electrically conductive silver-based compounds. To improve the piezoelectric performance of these synthetic membranes, the scientists have made them more porous, mimicking the porosity often seen in insect tympana.
The microscopic 3D variations in thickness, porosity, density, and pliability in the synthetic membranes help them behave like highly sensitive and efficient acoustic sensors. Their design helps them automatically filter sound in a mechanical manner, which means they do not require the power and computation needs of relatively bulky digital sound processors.
The team also believes that a mechanical way to separate different frequencies of sound with the precision of insects could prove useful for cochlear implants. Cochlear implants currently require digital signal processing, which involves receiving a sound, converting it from analog to digital, and processing the digital signal before stimulating the auditory nerve – all of which result in delays in hearing through the devices. If an implant can instead perform this frequency separation mechanically, “you can greatly reduce the delay,” Reid says.