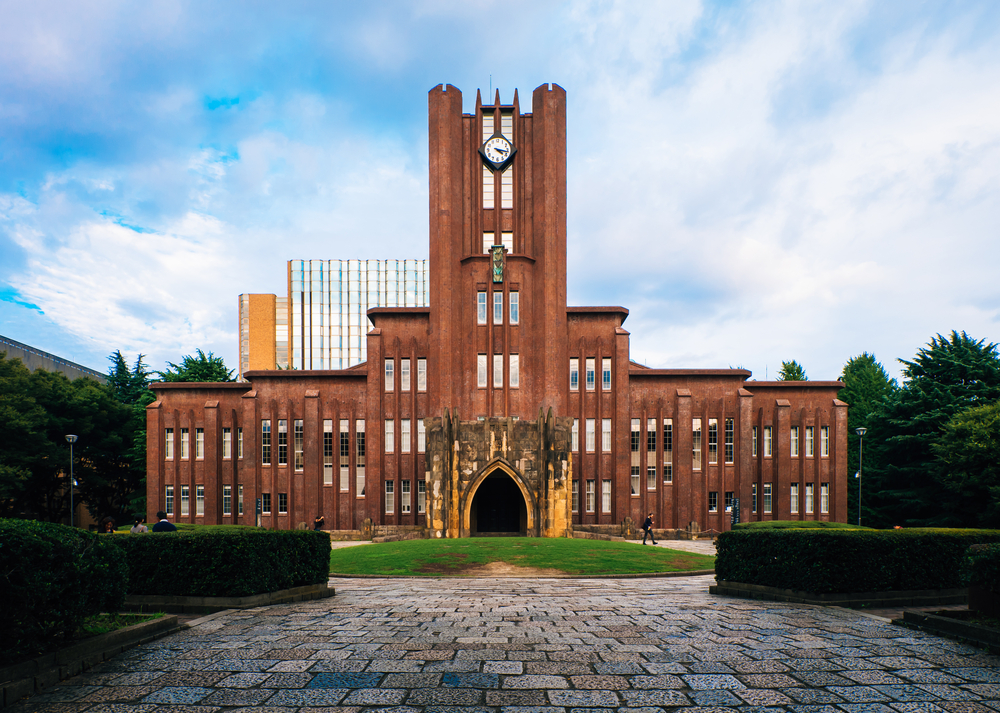
Material fatigue – the formation of cracks in a material due to cyclic loading – is a major concern in many industrial applications – especially for machine or airplane parts that experience many cycles of stress – when sudden failure could be catastrophic. Damage to industrial parts can be expensive, delay production, and can make the plant unsafe for workers.
Researchers at the Institute of Industrial Science at The University of Tokyo are using computer simulations to study the physical mechanisms of low-cycle fatigue fracture in the case of amorphous solids – such as glass or plastics. Their results have led to a better understanding of the underlying process of material fatigue.
It has been shown that preexisting defects and grain boundaries can initiate a fracture because of fatigue in crystalline materials, but the corresponding mechanism in amorphous materials has not been well understood. It has been assumed that the stress required for a fracture to occur is much smaller for cyclic stresses compared with constant stress, but the studies have shown otherwise.
“Contrary to the common belief, we showed that the critical strain in disorder materials that corresponds with the onset of irreversible deformation is the same for both fatigue and monotonic fractures,” says co-author Yuji Kurotani.
This tendency for material fatigue in ordinary amorphous systems is due to the higher density which leads to more elasticity and slower dynamics. This density dependence of mechanical properties couples the shear deformation with density fluctuations. The cyclic shear can then amplify density fluctuations until the sample breaks via cavitation, in which voids are produced.
“This situation is like a crowded train,” says co-author Hajime Tanaka. “Dynamic and elastic asymmetries with respect to density changes can lead to a link between shear deformation and density fluctuations.”
The authors of the study plan to confirm the computer simulations with experiments, with the expectation of helping material scientists better understand the initiation of fractures.